Understanding Injection Molding Plastics: A Guide for Manufacturing Success
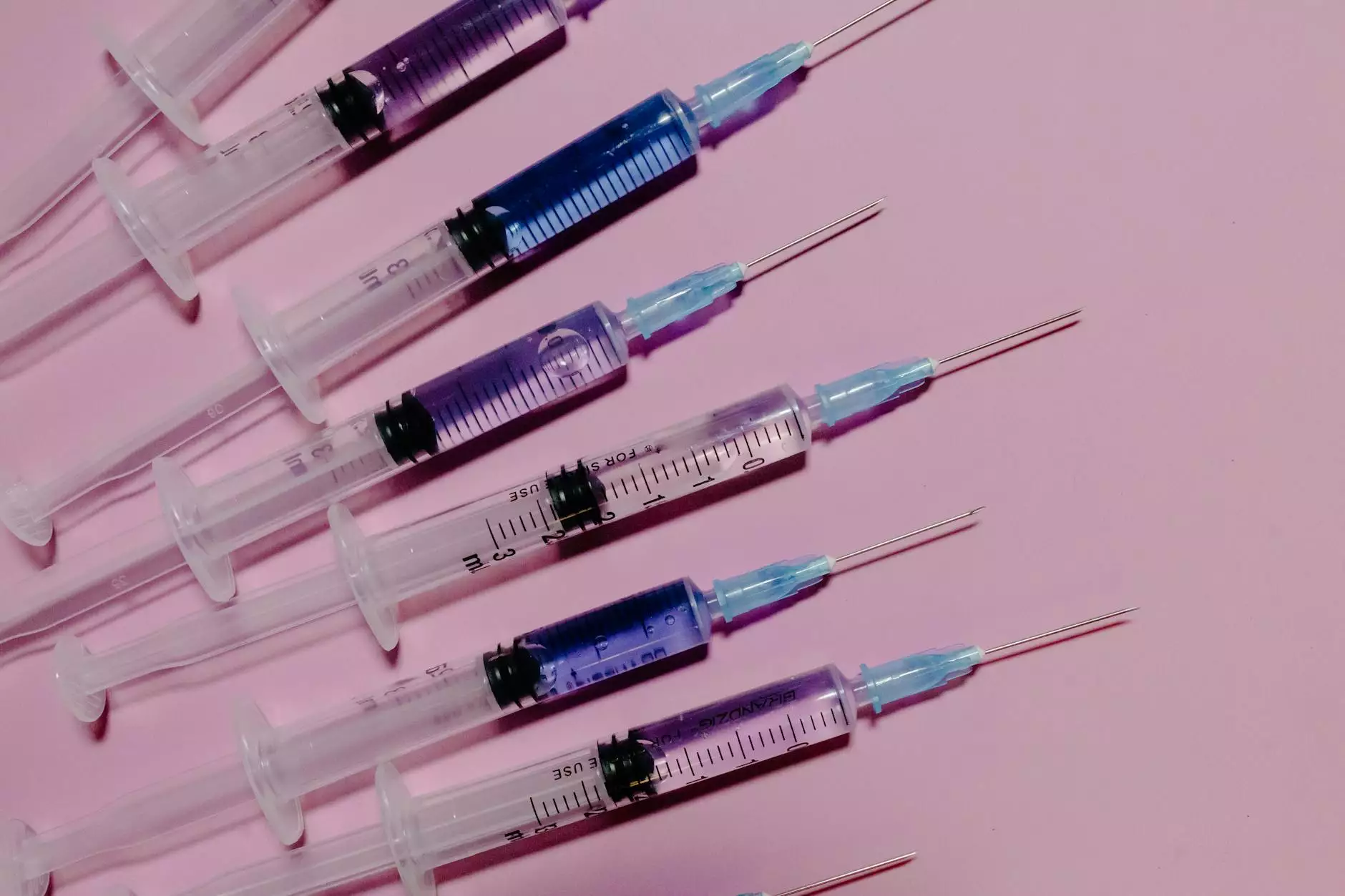
Injection molding plastics is a revolutionary manufacturing process that has reshaped industries by enabling the efficient production of complex plastic parts. From automotive components to household items, the versatility of injection molding plays a critical role in modern manufacturing. This article delves deep into the intricacies of injection molding plastics, illustrating its processes, advantages, applications, and future prospects in the industry.
What is Injection Molding?
Injection molding is a manufacturing process used to create parts by injecting molten material into a mold. The mold is then cooled and solidified, producing a plastic part with high precision and intricate detail. This technique is particularly advantageous for producing large quantities of identical parts efficiently and cost-effectively.
The Injection Molding Process Explained
The injection molding process consists of several key steps:
- Material Preparation: Plastic pellets or granules are first dried (if necessary) and then fed into a hopper.
- Melting: The material is heated until it transforms into a molten state in the barrel of the injection molding machine.
- Injection: The molten plastic is injected into the mold cavity by a reciprocating screw or a plunger.
- Cooling: The plastic is allowed to cool and solidify in the mold, taking its final shape.
- Ejection: Once cooled, the mold opens, and ejector pins push the finished product out of the mold cavity.
Key Advantages of Injection Molding Plastics
Injection molding offers a multitude of benefits that contribute to its widespread use in manufacturing. Some of the most notable advantages include:
- High Efficiency: The cycle times can be as short as seconds, allowing for rapid mass production.
- Cost-Effectiveness: Although the initial mold creation is expensive, the cost per unit decreases significantly with larger production runs.
- Precision and Consistency: Injection molding offers tight tolerances and uniform parts, reducing the need for post-production processing.
- Material Versatility: A wide array of thermoplastic and thermosetting materials can be used, including engineering plastics like ABS, polycarbonate, and nylon.
- Design Flexibility: Injection molding can create intricate designs and complex geometries that are often impossible with other manufacturing methods.
Applications of Injection Molding Plastics
Injection molding is utilized across various industries due to its versatility. Here are some notable applications:
1. Automotive Industry
The automotive sector employs injection molding for manufacturing components such as dashboards, panels, and clips. The process allows for lightweight parts that can enhance fuel efficiency while maintaining strength and safety standards.
2. Consumer Electronics
Injection molding is instrumental in producing casings for smartphones, laptops, and other electronic devices. The precision of the process ensures that complex designs are achievable while maintaining aesthetic appeal.
3. Medical Devices
In the medical field, injection molding plays a crucial role in creating components like syringes, surgical instruments, and diagnostic devices. The ability to produce sterile and highly precise parts is critical in this industry.
4. Packaging Industry
Many packaging solutions, such as bottles, containers, and lids, are produced through injection molding. The process's efficiency allows for high-volume production of lightweight, durable, and recyclable packaging.
5. Toys and Household Goods
Injection molded plastics are commonly found in toys and everyday household items. The ability to create vibrant colors and intricate shapes makes it ideal for these applications.
Choosing the Right Materials for Injection Molding Plastics
When it comes to injection molding, selecting the appropriate material is critical to the success of the project. The choice of injection molding plastics can dictate the mechanical properties, cost, and overall feasibility of the manufactured part. Here are some common materials used:
- ABS (Acrylonitrile Butadiene Styrene): Known for its toughness and rigidity; commonly used for automotive and consumer products.
- Polycarbonate: Offers high impact resistance and optical clarity; ideal for safety glasses and electronic components.
- Nylon: Renowned for its strength and durability; frequently used in applications requiring high wear resistance.
- Polypropylene: Lightweight, flexible, and resistant to chemical exposure; widely used for packaging and containers.
- PS (Polystyrene): A versatile plastic available in different forms; ideal for toys, household goods, and packaging.
Challenges in Injection Molding
Despite its advantages, injection molding is not without its challenges. Understanding these hurdles is crucial for manufacturers aiming to harness its potential effectively. Common challenges include:
- Mold Design Costs: Designing and manufacturing molds can be expensive and time-consuming.
- Material Selection: The wrong choice of materials can lead to defects such as warping or brittleness.
- Cyclic Variability: Variability in the injection process can lead to inconsistency in product quality.
- Maintenance: Regular maintenance of molds and machinery is necessary to prevent defects and ensure longevity.
Future of Injection Molding Plastics
The future of injection molding plastics is poised for significant advancements driven by technology and innovation. Some trends to watch include:
1. Advanced Materials
With the ongoing research in polymers, we can expect the introduction of advanced materials that possess superior mechanical properties and environmental friendliness, enhancing the applications and sustainability of injection molding plastics.
2. Automation and Smart Manufacturing
Automation technologies are set to revolutionize the injection molding process, allowing for increased production efficiency and reduced labor costs. Smart machinery equipped with sensors and AI can optimize the injection process in real-time.
3. Sustainability Initiatives
As the world moves towards more sustainable practices, the injection molding industry is adopting eco-friendly materials and processes. Innovations in recycling and biodegradable materials will play a pivotal role in decreasing the environmental impact.
4. 3D Printing Integration
The integration of 3D printing with injection molding processes is on the rise. This hybrid approach allows for rapid prototyping and the production of complex parts that can then be mass-produced using injection molding techniques.
Conclusion
In conclusion, injection molding plastics represents a fundamental technology in modern manufacturing. Its efficiency, precision, and versatility make it indispensable across various sectors. By understanding the process, materials, challenges, and future prospects, businesses can better position themselves to take advantage of this powerful manufacturing technique. Whether you are a manufacturer or a buyer, staying informed about injection molding plastics will enable you to navigate the ever-evolving industry landscape successfully.
For more insights and comprehensive solutions related to metal fabrication and injection molding, visit deepmould.net.