The Ultimate Guide to Plastic Injection Mould Manufacturing
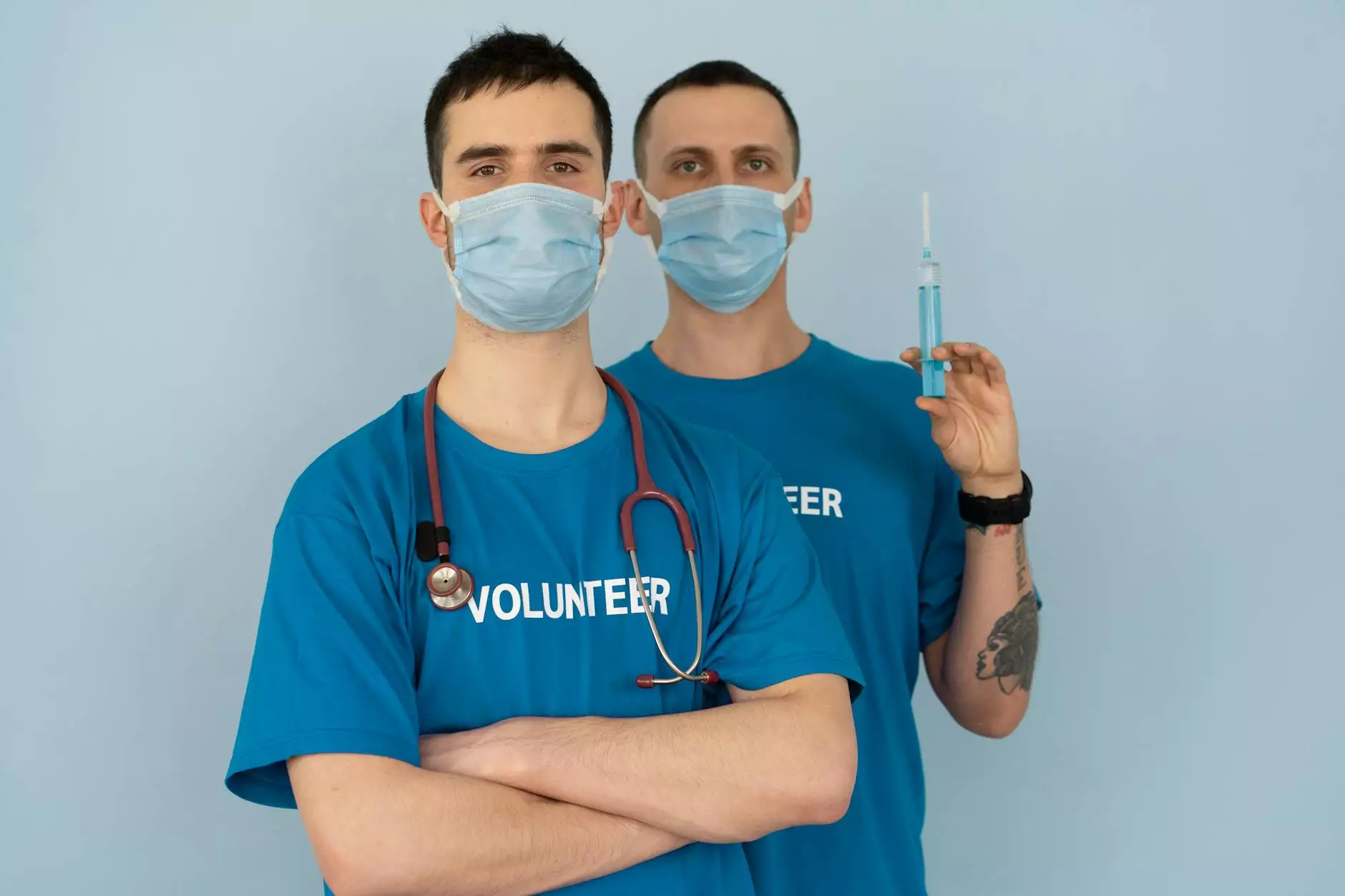
The world of manufacturing is ever-evolving, and among the pivotal players in this domain is the plastic injection mould manufacturer. Their role is crucial, providing the backbone for countless industries through innovative mold designs and techniques. This comprehensive guide will delve into the significance, processes, and innovations surrounding plastic injection molding, ensuring manufacturers stay ahead in today’s competitive market.
Understanding Plastic Injection Molding
At its core, plastic injection molding is a manufacturing process used to create parts by injecting molten plastic material into a mold. This method is favored for its ability to produce high volumes of precise components quickly and economically. Here are the key aspects:
- Efficiency: It allows for rapid production of intricate designs, making it ideal for large-scale manufacturing.
- Cost-Effectiveness: Once the initial investment in mold creation is made, the cost per part diminishes with increased volume.
- Material Versatility: A wide range of thermoplastics and thermosetting polymers can be utilized, allowing for different properties and finishes.
The Role of a Plastic Injection Mould Manufacturer
The role of a plastic injection mould manufacturer extends beyond just creating the molds. They are involved in every stage of product development, from the initial design concept to the final production of the molded parts. This includes:
Mold Design and Engineering
The process begins with the design of the mold, which requires a deep understanding of both the product specifications and the capabilities of the injection molding machinery. Skilled engineers utilize computer-aided design (CAD) software to create precise and detailed mold designs. Key factors to consider include:
- Durability: Molds must withstand high pressures and temperatures.
- Cooling Systems: Efficient cooling reduces cycle times and increases production rates.
- Draft Angles: These are critical for easy removal of parts from the mold.
Material Selection
The choice of material is crucial in the injection molding process. A successful plastic injection mould manufacturer understands the properties of various plastics, including:
- Polystyrene: Known for its rigidity and easy processing.
- Polyethylene: Offers excellent chemical resistance and is highly cost-effective.
- ABS: Provides a good balance of toughness and impact resistance.
The Plastic Injection Molding Process
Understanding the plastic injection molding process is essential for both manufacturers and clients. Here’s a step-by-step overview:
1. Material Preparation
Raw plastic pellets are fed into a hopper where they are heated and melted into a viscous liquid.
2. Injection
The molten plastic is injected into the mold cavity at high pressure, ensuring that every detail is captured accurately.
3. Cooling
The injected plastic is allowed to cool and solidify, taking the shape of the mold.
4. Ejection
Once cooled, the molded part is ejected from the mold using ejector pins.
5. Finishing
Post-processing may be necessary, including surface treatments, painting, or assembly with other components.
Innovations in Plastic Injection Mould Manufacturing
The industry is constantly advancing, and several recent innovations have significantly improved efficiency and product quality. These include:
Smart Manufacturing Technologies
Implementing smart manufacturing technologies, such as IoT-enabled machines, enhances monitoring and reporting capabilities. This allows manufacturers to:
- Track Production: Real-time data collection aids in identifying bottlenecks.
- Predictive Maintenance: Reduces downtime by predicting equipment failures before they occur.
- Quality Control: Automated systems ensure consistency and prevent defects.
Sustainable Practices
As industries move towards sustainability, plastic injection mould manufacturers are finding ways to minimize waste and energy consumption. Eco-friendly approaches include:
- Recycled Materials: Using recycled plastics in the injection process.
- Energy-Efficient Machines: Investing in machinery that consumes less energy.
- Waste Management Systems: Implementing plans for the recycling of defective parts and excess material.
Choosing the Right Plastic Injection Mould Manufacturer
For businesses looking to source quality plastic parts, selecting the right plastic injection mould manufacturer is critical. Here are several factors to consider:
Experience and Expertise
Evaluate the manufacturer’s experience in the industry. An established company is likely to have the knowledge required to handle complex projects.
Technology and Equipment
Investigate the types of technology and equipment they employ. Advanced machinery often translates to higher precision and efficiency.
Quality Assurance Measures
Inquire about their quality assurance procedures. A good manufacturer should have rigorous testing and inspection processes to ensure product quality.
Customer Support
Assess their customer support and communication practices. A responsive supplier can make the manufacturing process smoother and more efficient.
Conclusion
In conclusion, the role of a plastic injection mould manufacturer is imperative in the manufacturing landscape. By understanding the intricacies of the injection molding process, leveraging innovations, and selecting the right manufacturing partner, businesses can thrive in a competitive market. For those looking to explore further or initiate a project, Hanking Mould offers exceptional services as a leading plastic injection mold maker and manufacturer.