Understanding Plastic Injection Molds: A Comprehensive Guide
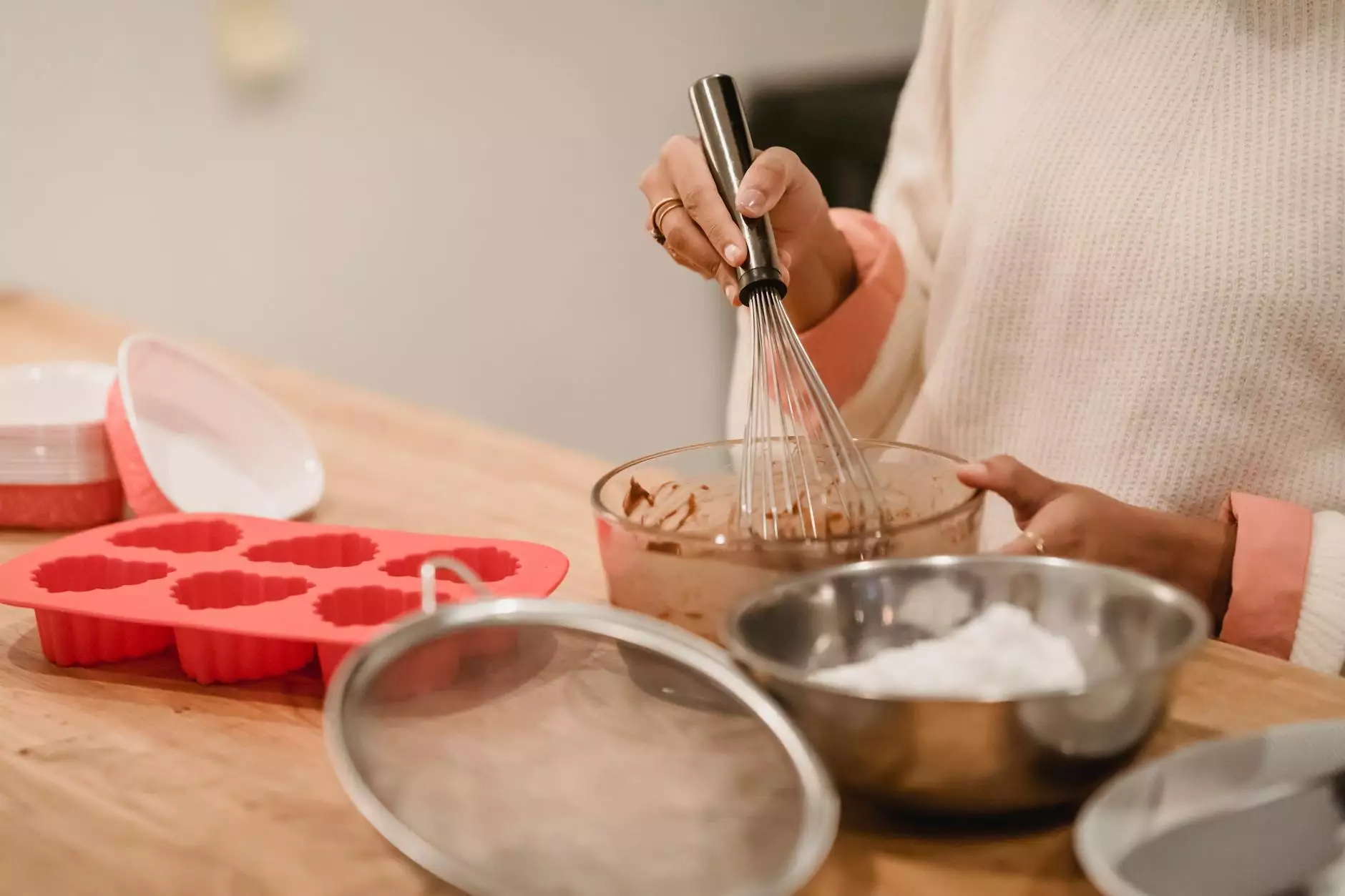
The world of manufacturing is vast, but few processes are as crucial as plastic injection molding. Whether you’re in the automotive industry, consumer goods, or medical devices, you’ll find that plastic injection molds play a pivotal role in producing high-quality products efficiently and cost-effectively. In this article, we will explore the ins and outs of plastic injection molds, focusing on their design, functionality, and the extensive applications within various industries. We will also touch upon how Deep Mould stands out as a premier provider in this space.
What are Plastic Injection Molds?
Plastic injection molds are tools used to create plastic parts by injecting molten plastic into a mold cavity, allowing it to cool and solidify into the desired shape. This process is highly efficient for mass production, as it enables the production of complex shapes with great precision.
The Process of Plastic Injection Molding
- Material Preparation: The process begins with raw plastic pellets being fed into the injection molding machine, where they are heated until they melt.
- Injection: The molten plastic is injected into the mold cavity under high pressure.
- Cooling: The molten plastic remains in the mold long enough to cool and solidify.
- Demolding: Once cooled, the molded part is ejected from the mold.
- Finishing: Any necessary post-processing steps, like trimming or surface finishing, are completed.
Benefits of Plastic Injection Molding
Choosing plastic injection molds offers numerous advantages, especially for businesses looking to streamline their production processes:
- Efficiency: High-speed production allows for thousands of parts to be produced within a short timeframe.
- Precision: Molds are designed with high accuracy, resulting in consistently uniform products.
- Versatility: Compatible with a wide variety of plastic materials, allowing for diverse applications.
- Cost-Effective: Over time, the efficiency of the process translates into lower per-unit costs, especially in high-volume runs.
- Complex Designs: Capable of producing intricate designs that would be impossible or costly with other manufacturing methods.
Applications of Plastic Injection Molds
Plastic injection molds are used in a plethora of industries, showcasing their versatility. Let’s explore some key sectors where they are integral:
1. Automotive Industry
The automotive industry relies heavily on plastic injection molds for manufacturing interior and exterior parts. Components such as dashboards, trim pieces, and light housings benefit from the durability and weight savings offered by plastic compared to traditional metal parts. This manufacturing method also allows for complex assemblies to be produced as single parts, reducing assembly time.
2. Consumer Goods
From toys to kitchen gadgets, consumer goods producers utilize plastic injection molding to meet high volumes of demand while maintaining quality. The flexibility of materials used allows for colorful and elaborate designs that attract consumers.
3. Medical Devices
In the medical field, precision and sterility are paramount. Plastic injection molds are used to create essential devices such as syringes, surgical instruments, and housings for electronic medical devices. These components frequently require custom molding capabilities to meet specific health regulations and standards.
4. Electronics
The electronics industry benefits from plastic injection molding by producing lightweight and insulated components such as housings, connectors, and parts for consumer electronics. The ability to create complex geometries with high precision translates into enhanced performance and reliability.
Design Considerations for Plastic Injection Molds
The design of plastic injection molds plays a critical role in the overall efficacy of the molding process. Here are essential design considerations:
1. Mold Design
Successful mold design requires an understanding of both the plastic material properties and the final part requirements. This includes factors such as:
- Draft Angles: Essential for ejection of the parts, preventing damage to the mold and the part.
- Wall Thickness: Consistent wall thickness is vital to ensure even cooling and prevent warping.
- Ventilation: Proper venting allows air to escape during injection, preventing defects.
2. Material Selection
Choosing the right plastic material is crucial as it impacts the part's strength, flexibility, temperature resistance, and other performance attributes. Common choices include:
- ABS: Known for its toughness and impact resistance, making it ideal for consumer goods.
- Polypropylene: Lightweight and chemical-resistant, often used in automotive applications.
- Polycarbonate: Offers excellent clarity and impact resistance, commonly used for electronic devices.
Deep Mould: Excellence in Plastic Injection Molding
Deep Mould is a leader in the field of plastic injection molds, known for its commitment to quality and innovation. Here’s why businesses choose Deep Mould as their trusted partner:
1. Advanced Technology
Deep Mould utilizes state-of-the-art technology to design and manufacture molds. Our innovative solutions ensure that clients receive molds that are not only durable but also optimized for the specific characteristics required for their production.
2. Customized Solutions
Understanding that one size does not fit all, Deep Mould offers tailored solutions based on client needs. Whether you require small batches or high-volume production, we have the expertise to deliver.
3. Experienced Team
Our team comprises highly skilled professionals with extensive experience in mold design and manufacturing. We work closely with clients at every stage of the process, ensuring that projects are completed on time and meet the highest standards.
4. Quality Assurance
At Deep Mould, quality is non-negotiable. Each mold undergoes rigorous testing and inspection to ensure it meets both industry standards and client specifications before it is dispatched.
Conclusion
In conclusion, plastic injection molds are a cornerstone of modern manufacturing across various industries. Their ability to create high-quality, complex components efficiently makes them invaluable for businesses. As industries continue to evolve and demand greater flexibility and precision, the importance of plastic injection molding will only grow. Partnering with an expert mold manufacturer like Deep Mould can provide your business with the competitive edge necessary to thrive in today’s fast-paced market.
For additional information about our services, or to discuss your specific molding needs, please visit Deep Mould’s website today.